Product Information:
A) Gentle Blowroom Line
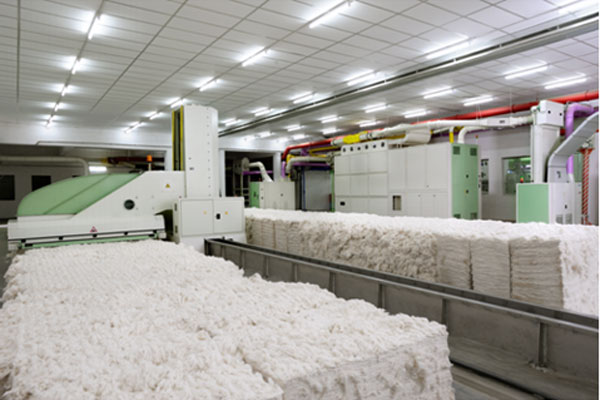
- Higher Productivity
- Consistent quality
- Varying fibre characteristic
- Gentle Blowroom Line with opening, cleaning & Homogeneous blending
- Highly Flexible Blowroom Line which assures highest cleaning efficiency and raw material realization
- Electronic control for waste adjustment
- Blending solution assures high accurate blending upto 1% range
- Integrated microdust extraction principle
(i) Baleplucker LA23/S
Features- Higher Production upto 2000 kgs/hr
- Twin plucking roller in operation during machine running ensures minimum tuft size which makes the subsequent process most effective with gentle opening & cleaning
- Traverse Speed up to 20 mts/min
- Inbuilt magnet & seed trap arrangement for effective removal of foreign materials
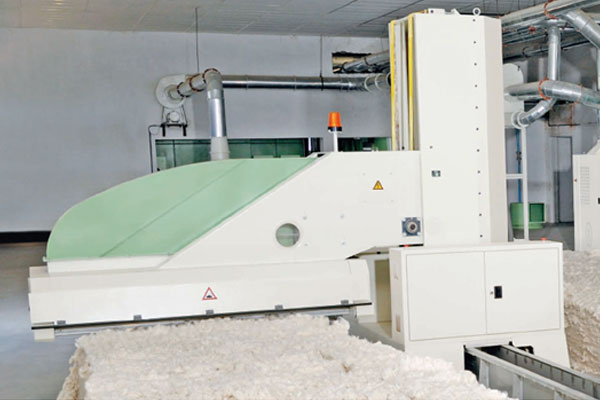
- Suitable to process upto 4 assortments
- Automatic varying of plucking depth based on the density of the bale and assortment
- Track length of 10m to 50m in steps of 2.5m
- Capable to work on both the sides of the track
- Easily replaceable plucking strips
- Auto scanning
- Increases the machine utility and efficiency
- Elimination of skilled manpower
- PLC Controlled movements and positioning
- Inverter drive for all positions and movements
- Gearless drive for turning of Plucking head
- Chainless drive for Tower Positioning movement
- Automatic turning of head
- Optional light barriers arrangement which stop the machine in case of any interference
(ii) Swift Floc LA21
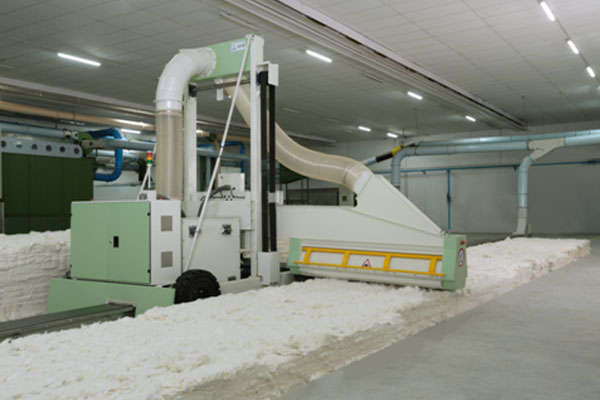
The Swift Floc LA21 is built and incorporated with new features. The aim is to provide the industry with an automatic machine at economic value. The Swift Floc, with its user-friendly construction, brings down the production cost (per kg of delivered material) to a great extent.
Features- Machine with production capacity up to 600 kg/hr
- The smallest tuft with a high degree of opening is achieved by the dual directional plucking roller. The tufts thus opened can be efficiently cleaned by removing dirt and microdust extracted to the maximum extent, in the downstream machines of the blowroom.
- Unique Design of Pluckign Teeth - Specialized angle of plucking tooth and grill arrangement ensure that plucking is uniformly done throughout the bale lay down.
- Suitable to process 2 assortments
- Fixed cover belt on suction canal for material transportation
- Trolley movement with automotive tyres
- Inverter driven plucking roller, which rotates in dual direction
- Inverter for Lif ting and Linear movement
- Optional light barriers arrangement which stop the machine in case of any interference
(iii) Vario Clean LB 9/2
- Higher Production up to 1600 kg /hr
- Higher Cleaning Efficiency is achieved with Specially designed beater element for gentle cleaning and effective opening
- Effective micro-dust and seeds removal by free beating along the surface of the opening roller
- Dynamic setting changes for different assortments
- Machine is inbuilt with Opening, cleaning and de-dusting functions
- The grid bar selection can be made based on High & Low Trash
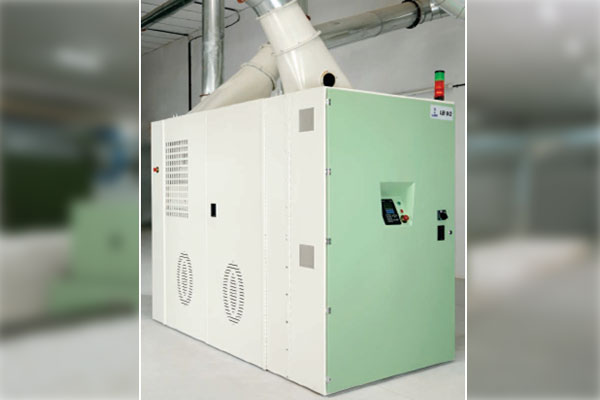
- Inverter driven plucking roller, which rotates in dual direction
- Inverter for Lif ting and Linear movement
- Optional light barriers arrangement which stop the machine in case of any interference
(iv) Unimix LB 7/4
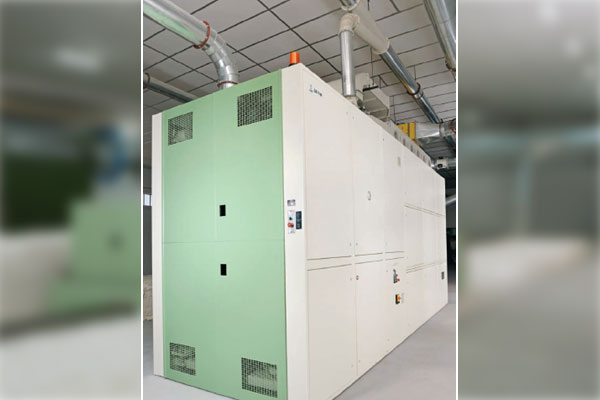
- Higher production upto 800 kg/hr
- Enhance the value of mixing through
- Homogeneous blending
- Efficient opening and cleaning
- Flexible grid bar setting
- Machine has 6 chambers with larger storage capacity ensures regular and uniform feeding of the downstream machines
- All types of cottons, man-made fibres and their blends can be processed with or without cleaning point
- Wide range of opening rollers from Disc to Needle for different fibre applications
- Can feed directly to next cleaning machine or to card while processing mixing for fine count
- Continuous feeding of material to card ensure uniform filling in chute
- Inverter control drives with speed change through display
(v) Unimix LB 7/6
- Higher production upto 1000 kg/hr
- Enhance the value of mixing through
- Homogeneous blending
- Efficient opening and cleaning
- Flexible grid bar setting
- Machine has 8 chambers with larger storage capacity ensures regular and uniform feeding of the downstream machines
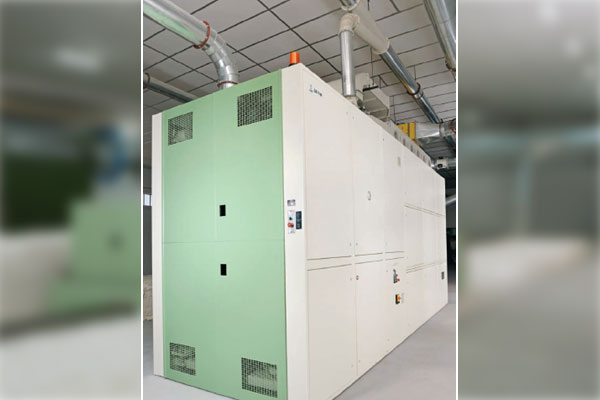
- All types of cottons, man-made fibres and their blends can be processed with or without cleaning point
- Wide range of opening rollers from Disc to Needle for different fibre applications
- Can feed directly to next cleaning machine or to card while processing mixing for fine count
- Continuous feeding of material to card ensure uniform filling in chute
- Inverter control drives with speed change through display
(vi) Flexi CLean LB 5/6
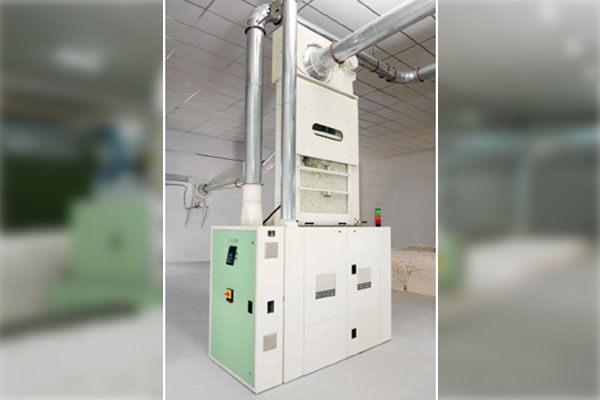
- High production up to 600 kg / hr
- Variable production achieved by inverter drive
- Controlled fibre feed for optimum opening and maximum cleaning efficiency
- Adaptable for different types of opening rollers
- Ensures gentle opening and maximum cleaning efficiency for wide range of fibres
- Adaptable for different types of opening rollers
- Inverter control drives with speed change through display
(vii) Supremoclean LB 10/2
- Higher production upto 1000 Kg/hr
- Increased working width of 1600 mm
- Trio Feed roller for better compacting
- Adaptable for different types of opening rollers
- Ensures gentle opening and maximum cleaning efficiency for wide range of fibres
- Continuous feeding of material to card ensure uniform filling in chute
- Automatic grid bar to beater setting
- Inverter control drives with speed change through display
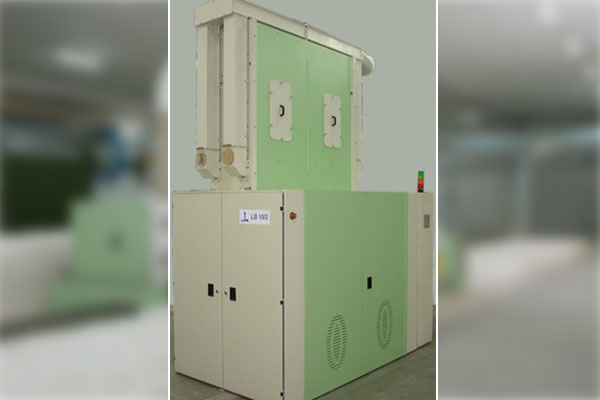
B) Card LC 363 / LC 361
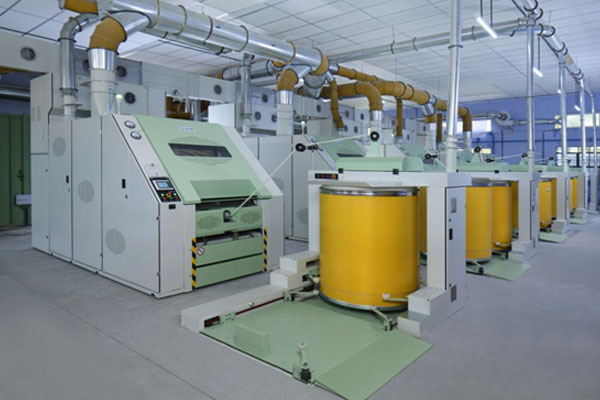
Card LC363 / LC361 is designed for higher production up to 150 kg/hr with distinctive features to produce high quality sliver in every variety of cotton, man-made fibre and blends. “Well carded is half spun”. Card LC363 / LC361 is configured to produce better yarn characteristic with reduction in running cost.
Features- Triple / Single Licker-in arrangement
- Special profiled Arcual combing arrangement for lesser lint loss
- Card with Highest number of working flats (36 nos.)
- Highest Active Real Carding Area 1.296 mtrs - 20% higher carding area
- Higher stability through lower thermal expansion material
- Online Quality Monitoring System (QMS)
- Linear can Changer for higher utilization
- Variable nipping distance for gentle fibre opening
- Interchangeable and addition of Pre & Post carding elements and Knife positions
- Replacable type polymer end connector
- Specially coated coiler for processing MMF
- Unique wire profiles for effective carding action for processing OE, Regenerated, Airjet & MMF Process
- High speed take up Conveyor web doffing arrangement
- Pressure regulated chute for uniform Feeding
- Inverter control cylinder drives with speed change through display
- Integration of Cards through SPINCONNECT
C) Card LC 636
‘Card With Highest Active Carding Area & Cylinder Area’ Increased Production With Optimal Utilization Of Resources The quality of the card sliver has a substantial impact on yarn output. Well carded is therefore, half spun. LMW’s Card LC636 is a step forward in the company’s journey of breaking barriers and setting new standards in achieving consistent quality with higher precision. The LC636 handles cotton, blends and man-made fibres with ease. With the highest active carding area of 1.95 sq. m. and a cylinder area of 3.95 sq. m. LC636 scores high on user-friendliness, promising long-term value to the customer.
Features- Special profiled Arcual combing arrangement for lesser lint loss
- Card with Highest number of working flats (36 nos.)
- Highest Active Real Carding Area 1.95 m2 and Highest Active Cylinder Area 3.95m2
- Higher stability through lower thermal expansion material
- Online Quality Monitoring System (QMS)
- Linear can Changer for higher utilization
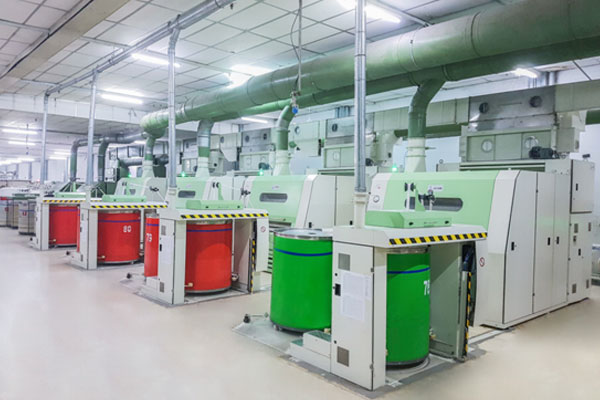
- Variable nipping distance for gentle fibre opening
- External knife adjustment for easy licker-in dropping optimization
- Interchangeable and addition of Pre & Post carding elements and Knife positions
- Replacable type polymer end connector
- Specially coated coiler for processing MMF
- Unique wire profiles for effective carding action for processing OE, Regenerated, Airjet & MMF Process
- High speed take up Conveyor web doffing arrangement
- Pressure regulated chute for uniform Feeding
- Inverter control for Lickerin & cylinder drives with speed change through display
- Integration of Cards through SPINCONNECT
A) Draw Frame LD2
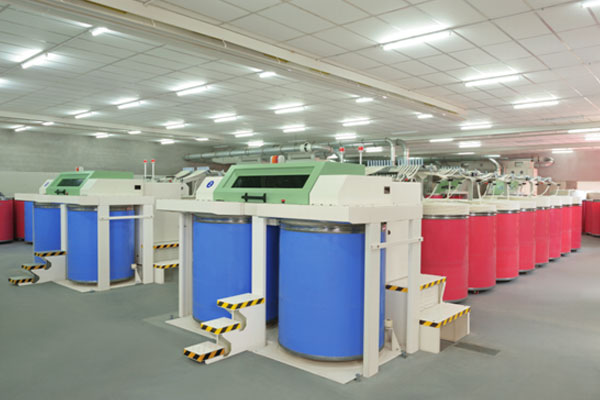
The newly designed twin delivery high speed non Autoleveller DrawFrame LD2 with automatic can changer (for cans of upto 600 X 1200 mm or 24" X 48") enables the spinner to reduce the cost of production considerably. Also the LD2 DrawFrame without the can changer feature (for delivery cans of size 1000 X 1200 mm or 40" X 48") has its own advantages.
Features- Delivery speed of upto 1000m/min (mechanical). Technologically upto 800 m/min
- Spring loaded 4 over 3 pressure bar drafting arrangement for controlled fibre flow
- Timing belt drive for noiseless transmission
- Ergonomically designed creel for accommodating feed cans upto 40” diameter
- Delivery Can Size of 20” x 45” / 48”, 24” x 48” with automatic can changer
- Delivery Can Size of 40” x 48” with can pusher
B) Lap Former LH 15
The design of the technological components plays an impor tant role in enhancing the productivity of the machine. In Lap Former LH15, the patented lap roller profile and its optimized groove guarantees a constant average speed for all counts. Double optimized grip by lap roller ensure better lap formation. This is a major contributing factor for high productivity of upto 520 kg/hr.
Features- PRO-IN control system for better lap preparation
- Average delivery speed up to 150 m/min (depending on raw material)
- Production of up to 520 kg/hr
- User friendly touch screen display for better navigation
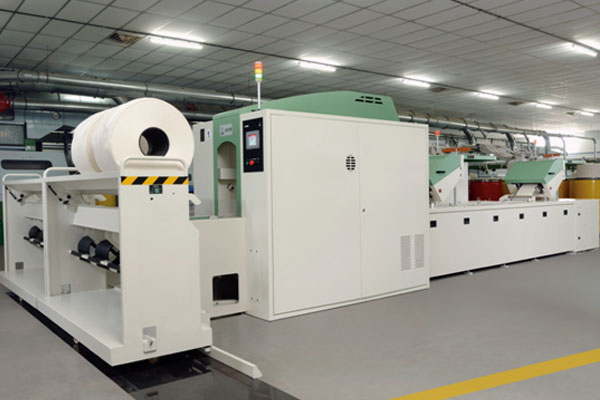
- Ergonomically designed positively driven creel for sliver feed with sensor activation control through display
- Automatic lap doffing with Minimum doffing time ensures higher efficiency and productivity
- Lap Transport System feature helps automatic transfer of prepared lap from Lap Former to Comber without manual intervention, thus saves considerable amount of time and inventory cost.
C) Comber LK64Z
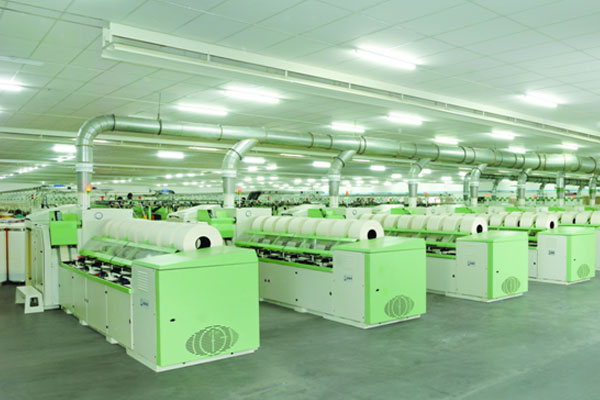
Comber LK64 Z with technological speeds of upto 500 NPM, incorporated with (MCDP Plus) is designed to produce upto 1.7 tons/day of combed sliver. This technology, combined with specially profiled, light weight aluminium alloy Nippers and reduced number of moving parts, assists high speeds and productivity
Features- Speed up to 500 npm (Technological)
- Production up to 1.7 Tons/day
- Mathematical Modelling of Combing Dynamics & Process PLUS Technology (MCDPPlus)
- 3/3 pneumatically loaded drafting system
- Specially profiled light weight aluminium alloy nippers
- Piecing assistance in drafting zone
- Modular construction
- Suitable to extract wide range of noil (based on Raw Material and End Quality requirement)
- Automatic spool change from Lap trolley to comber
D) Comber LK69
Comber LK69 with “PACT”, “Sets the pace”, in the combing technology with a production of up to 2.1 Tons/day @ 600 npm. The kinematical linkage syntheses for synchronized and optimal movement of parts ensure gentle handling of heavier laps. The optimal selection of fibre enables the machine to run at higher speeds without straining the fibre and ensure efficient removal of short fibres.
Features- Production up to 2.1 Tons/day
- Speed up to 600 npm
- PACT for versatile operation
- 3/3 pneumatic load inclined drafting system placed over the coiler for direct entry of sliver to coiler calender roller
- Specially profiled light weight aluminium alloy nippers
- Piecing assistance in drafting zone
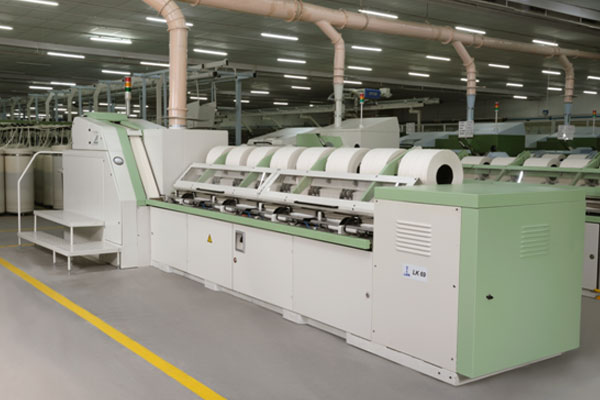
- Can changer with two reserve Cans for 24” delivery
- Can changer with one reserve Can for 40”delivery
- Modular construction – with 2 modules
- Suitable to extract wide range of noil (Based on raw material and End quality requirement)
- Automatic spool change from Lap trolley to comber
- Servo/Inverter control drives for Draft/speed change through display (Optional)
E) Draw Frame LDF3
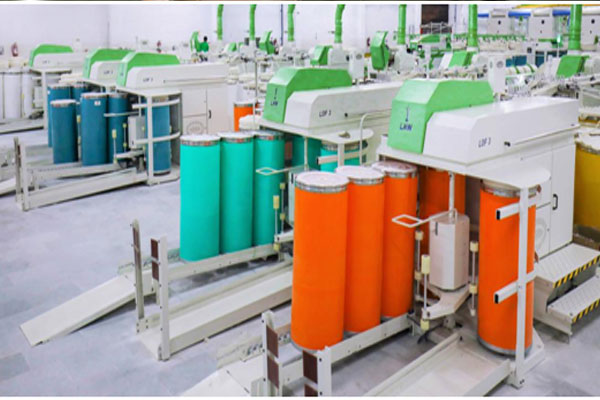
The newly developed Autoleveller Drawframe LDF3 is equipped with best in class in features like Servo draft, change gearless main motor, Auto piecing along with online sliver monitoring. Since LDF3 delivers benchmark quality at affordable price, it became instant success among customers.
Features- Change gearless drive
- Servo draft- Elimination of differential gear box
- Top roller end bush with sealed bearing and Lifetime grease
- Self cleaning Top roll stripper - TR STRIP
- Integrated suction system for drafting, console and sliver feed at scanning
- Ergonomically designed four row creel for accommodating feed cans upto 40’’ dia
- Filter box with wiper arrangement for easy maintenance
- Spectrogram for self diagnosis of mechanical faults
- Electronic sliver cutting- Suitable to process all kind of raw material without manual cutter arrangement
- Replaceable stainless steel coiler for man-made fibres provides the luxury of changing only coiler plate instead of entire set
- Option of adjoining platform for space saving execution
- Auto piecing to restart the machine smoothly after any machine stoppages due to delivery area
- Delivery can dia from 12’’ (300 mm) to 24’’ (600 mm) with rotary can changer arrangement
- Inverter control drives with speed change through display
Suction Compact System - “SPINPACT”
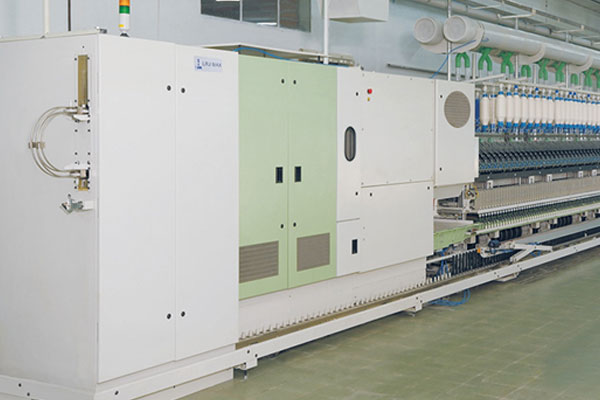
Spinpact- LMW Compact System is developed for achieving Superior Productivity with Unrivalled Quality and Energy Efficiency. It is an Ultimate Compact System to produce a fully Compacted yarn for different applications of Weaving and Knitting.
This Innovation from LMW helps in ease of operation and ease of maintenance thus improving the overall effective utilization of the system.
- Positive driven perforated apron for better compacting
- Suction nozzle with unique cross section made with Special Aluminium alloy
- Eight Spindle drive for enhanced suction management and easy maintenance
- Top suction system for user friendliness
- Special geometry for prolonged compacting and hence matchless lower hairiness and better strength of yarn
- Different tension drafts for processing Cotton and MMF
- Can be retrofitted in all Ring frame models
- Ready to make single and SIRO compact
- Inverter controlled Compact Suction motor to adjust & fine-tune the required Compact suction pressure
SPINCONNECT
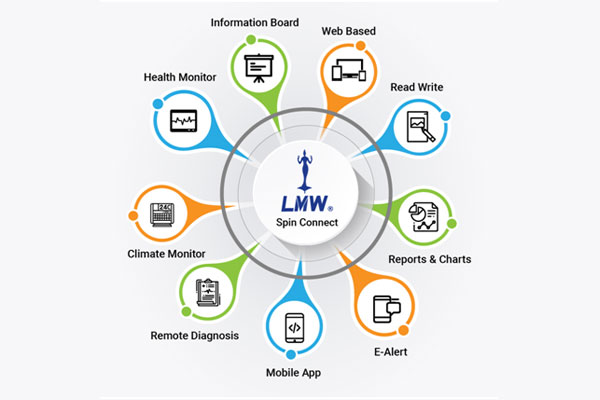
LMW Spinconnect is a web based monitoring and control application which networks the process from Blow room to Winder.
This system captures and displays parameters like Speeds, Production Stoppages, Quality, Power etc.
Helps in close monitoring of Plant Utilization and Productivity levels.
- System is built with four modules called Production module, Energy module, Health monitoring module, Spindle monitoring and Roving Stop Motion (YBS & RSM) module
- Spin connect is equipped with unique Recipe management system which helps in streamlining and improving the Process in easiest way
- Web based system helps in connecting system anytime anywhere through Laptops,Computers,Tablets & Mobile phone
- All the previous data can be retrieved and can be used for analysis and comparisons
- Simpler connectivity of system results in easier maintenance
- Data base is like an encyclopedia of the plant which further useful in achieving better productivity with better quality at minimal production cost.
- All the older version and latest version machines of LMW can be connected
- Connectivity of the entire system can be done through LAN or WiFi
- All the variable parameters in machines can be changed from any where even through mobile phones. This helps in implementing quicker solution and also reduces the machine downtime
Lakshmi Winder LW72
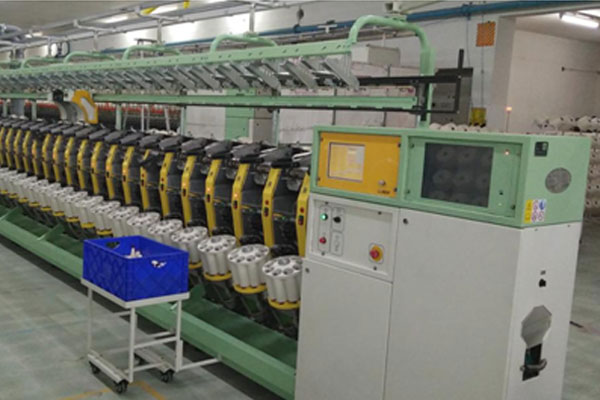
- Number of winding heads upto 72
- Maximum Mechanical speed 2000 m/min
- Digital Signal Control (DSC) technology
- Square shaped unwinding accelerator
- Protection for abrasive yarn winding
- Electroless nickel plated grooved drum
- Machine computer with inbuilt UPS and 15” touch screen for HMI
- Wide range of Customized reversal speed
- Twin Doffer option for counts below 20s
- Wider band reversal speed for easy manipulation of splicing cycle Min 30mpm max 70mpm
- Inverter controlled Closed loop suction management system
- Automatic Doffer Arrangement
- Waxing system with wax exhaust detection
A) Speed Frame LF1400A
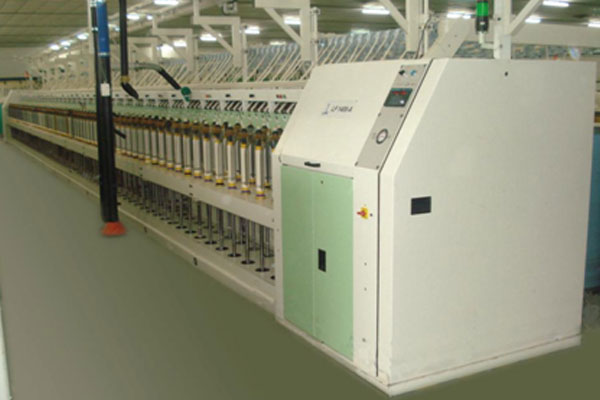
- Maximum spindles up to 144
- Positive Top and Bottom clearer system
- Effective suction system for both top and bottom clearer waste
- Dual compartment filter box
- Electro magnetic device for reliable trough reversal
- Simplified 3 roller and 4 roller spring loaded Drafting system
- Creel up to 7 rows for easy accessibility
- Inverter controlled Main motor to adjust the Spindle speed through display.
B) Speed Frame LF4200 Series
All the drives of Bobbin,Flyer,Bobbin trough and Drafting are driven by Servo motors.The machine can be easily clubbed with Roving Transportation System by installing bobbin converters in any of the sides of the machine.Automatic Tension Control system ensures the uniform and consistent tension of the roving and thus delivers perfect roving packages with Supreme quality.
Features- Upto 280 spindles for both cotton & Man Made Fibres
- Detachable flyer spindle for removing bobbin in midway
- Dual & split drive concept
- CQ duct for effective and consistent suction through out the machine
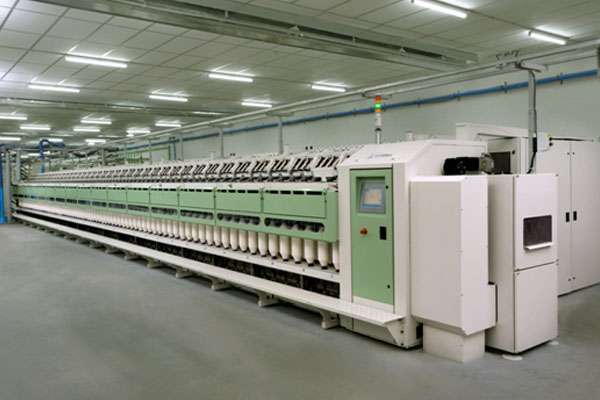
- Provision to drive sectional segments(40 spindles)
- Ready to doffer retro-fitment in future
- Special Bobbin Tilting mechanism for ease of operation
- 3/3 & 4/4 drafting system option available, In 4/4 drafting system both 2nd roll apron drive and 3rd roll apron drive option available
- Flyer size of both 6”X 16” & 7”X 16” option available
- 4 Row/5 Row/6 Row Hexagonal creel available
- Availability of Pneumatic and Spring loaded drafting system
- Both pneumatic and spring loaded drafting system option available
- Rapid doff system with lesser doff time ensures more productivity
- Bobbin Exchanger can be fixed on either end of the sides
- Provision to connect with Roving Transportation system
- Draft,Speed,TPI change through display
- Ready to merge with LMW Spin Connect system
C) Speed Frame LF4280 Series
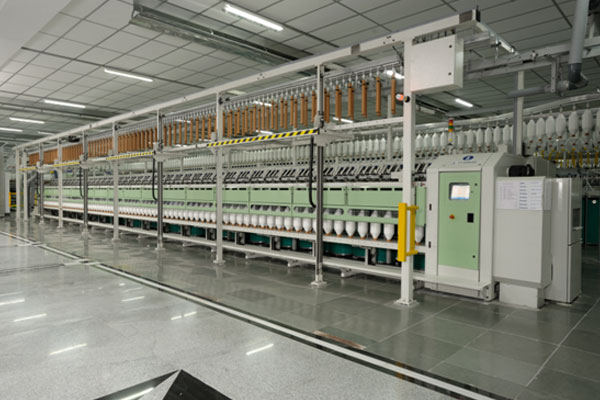
All the drives of Bobbin,Flyer,Bobbin trough and Drafting are driven by Servo motors.The machine can be easily clubbed with Roving Transportation System by installing bobbin converters in any of the sides of the machine.Automatic Tension Control system ensures the uniform and consistent tension of the roving and thus delivers perfect roving packages with Supreme quality.
Features- Upto 280 spindles for both cotton & MMF.
- Drafting drive through servo motors.
- Effective & Uniform suction with CQ duct arrangement.
- Detachable flyer spindle for removing bobbin in midway.
- Monitoring of drives/motor parameters through Display
- Dual & split drive concept.
- Provision to drive sectional segments (40 spindles).
- Ready to doffer retro-fitment in future.
- Special Bobbin Tilting mechanism for ease of operation
- 3/3 & 4/4 drafting system option available, In 4/4 drafting system both 2nd roll apron drive and 3rd roll apron drive option available
- Flyer size of both 6”X 16” & 7”X 16” option available
- 4 Row/5 Row/6 Row Hexagonal creel available
- Both pneumatic and spring loaded drafting system option available
- Rapid doff system with lesser doff time ensures more productivity.
- Bobbin Exchanger can be fixed on either end of the sides.
- Provision to connect with Roving Transportation system.
- Draft,Speed,TPI change through display.
- Ready to merge with LMW Spin Connect system.
- Monitoring of Power consumption in display
D) Ring Frame LR9 A/AX/AXL Series
LMW proven spinning geometry enhances the quality and productivity. LMW Ringframes with robust design helps in less maintenance cost, machines with inbuilt Energy saving solution to ensure less Spinning cost and boosts Profitability to Spinners.
Features- LR9A upto 2016 spindles helps in less space requirement, less humidification comparatively
- Hook Lock Low Decibel (HLLD) spindles with less Vibration & Noise
- In built Energy saver with IE4 main motor, Inverter Controlled IE3 suction motor,Inclined suction tube to improve effective suction
- 4Q-2M drive for drafting
- T-Flex drive system for quality consistency
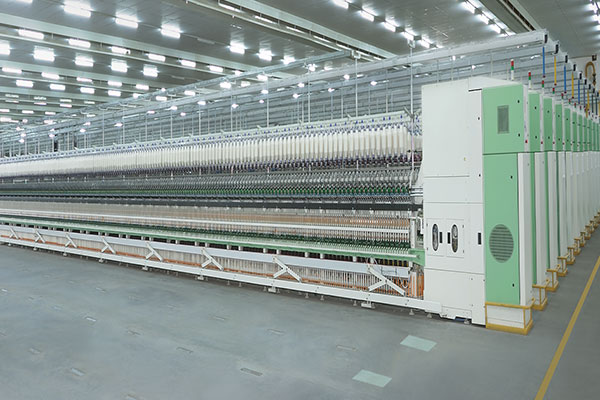
- Ne range from 8s to 200s can be spun
- Machines with doffer and without doffer option available
- 16 step Speed pattern curve
- Ready to retrofit of Compact/SIRO system
- Spindle pitch 70mm & 75mm option available with lift options from 160 to 240mm
- Pneumatic load and Spring load both the options of Top arm are available
- Rapid doff system (<100sec doff time)
- Basket Tube loading system for ease of operation
- Yarn Breakage monitoring system & Roving stop motion available as optional
- Machine ready to merge with LMW Spin Connect system with an unique feature called Recipe management
- Power Consumption can be monitored through display
E) Ring frame LR9SX/SXL Series
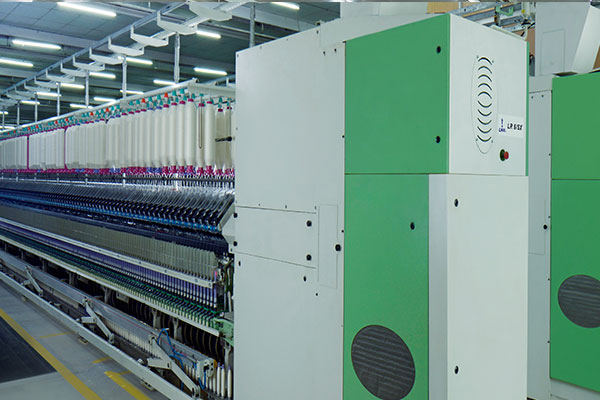
This series of LMW ring frames are designed with innovated technology for versatility in product. All Superlative features of this series make it as a Gen-Next machine. All parameters including draft are changeable by simple screen touches and also ability to start quadrant wise make the machine user friendly. The technology ensures the Spinning of yarn with value addition for Profitability in maximum level.
Features- LR9SX up to 2016 spindles helps in less Capex
- Credo+ Rings ensure better performance
- HLLD spindles with less Vibration & Noise
- Polymer Jockey Pulley with life time grease ensures less maintenance
- Inbuilt Energy saver with IE4 main motor,Inverter controlled IE3 suction motor & Inclined suction tube arrangement
- LMW’s unique T-Flex, 4Q-2M drive concept
- Inbuilt YBS, RSM for enhancing the performance
- Slubs like Vario slub,Negative slub,Slub on slub,Short slub,Injection slub can be spun
- Fancy yarns like Multi Twist, Multi Count, SIRO can be spun
- Four Quadrant drive system for easier restarting of machines after material changing
- Ready to retrofit of Compact system
- Spindle pitch 70mm & 75mm available with lifts from 160mm to 240mm
- Rapid doff system (<100sec doff time)
- Rogue spindles, Slip spindles, Idle spindles can be identified through YBS &RSM system
- Machine ready to merge with LMW Spin Connect system with an unique feature called Recipe Management
- Power consumption can be monitored through display
- Dedicated software to preview Slub pattern